Epson robots are built for this type of operation, and for any manufacturing process that’s fast, repetitive, and uses a high volume of smaller parts.”
That’s Tim McArthur, vice president of manufacturing services and quality at Delta Systems Inc. in Streetsboro, OH, explaining why he uses SCARA and six-axis robots from Epson America Inc. to assemble electronic components for industrial equipment. Diy Hydraulic Arm
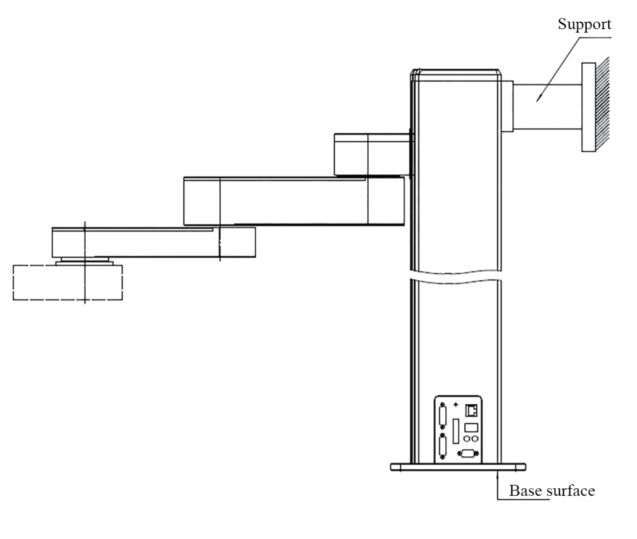
McArthur has been employing Epson robots since 2017, when an integrator, Great Lakes Automation, supplied some for two separate operations. “We trusted their expertise and did our own research and decided we would move forward with Epson as we designed our own systems in house,” he says.
Today, Delta Systems uses more than 20 Epson robots for pick and place, assembly, dispensing and soldering operations. The company has also integrated an Epson IntelliFlex parts feeding system to move parts into a system that assembles key switches for lawn tractors, producing almost 2 million switches each year.
“We are standardizing on Epson wherever we can. In about 80 percent of the robotic operations in our factory, Epson is easily the top pick for us,” says McArthur.
Delta Systems manufactures switches, meters, controllers and displays for outdoor power equipment, utility vehicles, agricultural and light industrial machines and vehicles. Among its clients are John Deere, Toro, Ryobi, Honda Power Equipment, Kawasaki, Bombardier and Husqvarna. The company does all of its manufacturing in a 150,000-square-foot plant in Streetsboro, which employs about 215 people.
One example of its processes is an operation that builds hour meters for tractors and utility vehicles. These meters are small assemblies with a 1-inch diagonal LCD display that notify users when it’s time to change the oil and perform other maintenance.
“We are soldering a tiny piece of metal onto a printed circuit board, and that must be done in a very accurate manner,” McArthur explains.
To assemble these meters, Delta employs two Epson T6 SCARA robots to pick and place parts and three more to solder them together.
“One T6 robot places the parts onto a large dial, which rotates them over to the soldering robots. All three robots work on solder joints at the same time,” says McArthur.
Next, another T6 robot removes the finished assembly from the dial. Depending on the being assembled, each robot may create three or four solder joints on a board.
The challenge in this operation is speed and precision, with the robots working together to complete 750,000 meters per year, with at least 2.25 million solder joints.
Prior to 2020, Delta had used an off-the-shelf robotics system built specifically for soldering. But as that system approached the end of its useful life, McArthur and his team felt they could build a system in-house that performed just as well, and at a much lower cost.
“There are probably three or four companies that specialize in robot soldering, so buying an off-the-shelf system would not have been a problem,” McArthur explains.
Yet he felt that, with the company’s industrial automation experience, it would be better off building its own system. It took about six months for the engineering team to design and fabricate the new soldering setup, with about one week devoted to installing and programming the new robots, each with a commercially available soldering head.
“The most difficult part of the process was to get the different parts to communicate,” McArthur says. “And when I say difficult, that was mainly because we had never done it before.”
While the Epson robots began talking to the soldering heads immediately, the “handshake” was challenging because the soldering system uses proprietary communications protocols. “We worked with Epson on the issue, and I have to say its support is every bit as good as its equipment,” says McArthur.
In the end, merging the Epson robots with the soldering heads in-house saved Delta Systems about half the price of an off-the-shelf soldering system. “Typically, we save at least 35 percent when we integrate an automation system ourselves, but in this case it was more like 50 percent,” says McArthur.
There were additional savings as well. One common difficulty with robotic soldering is the need to frequently adjust the movement of the robot, as the attached soldering tool changes shape with wear. “Over the course of a week, we might do 50,000 solders,” McArthur notes.
With the previous system, making the adjustment was complicated enough to require an automation engineer. If it was needed when an engineer was not available, say, on an overnight shift, then the operation would have to shut down.
To address the problem, the team purchased an Epson TP1 teach pendant, which makes it easy to teach the robot the various points it must navigate to perform its functions.
“With the teach pendant in hand, an operator can move the robot to a point, check the alignment, adjust it as needed and then save the adjusted point into the program,” says McArthur.
Not only are operators avoiding downtime with the teach pendant, but they’re able to save 10 to 15 percent of the cost of expensive soldering heads, because they’re using them longer with the simplified adjustments, McArthur points out.
After the team had finished the installation and Delta Systems began using it to manufacture hour meters, “our third-party integrators came in and wanted to look at it, because they get requests for that kind of system all the time,” says McArthur.
Moving forward, McArthur says Delta Systems will continue to use Epson SCARA and six-axis robots anywhere speed and precision are important considerations.
There are three reasons McArthur prefers Epson robots.
“Epson has been able to build a robot that is as accurate as we need it to be and as fast as we need it to be,” McArthur explains. “That’s No. 1. They just fit what we do here.”
The second reason is cost. McArthur says that’s not just the cost of the robot, but the fact that it’s simple enough to integrate that his team can do it in-house.
The third reason is service. “Our local technical distributor, Grant Schiefferle, with Factory Automation Components, has been fantastic,” says McArthur. “And Chris Round, our regional manager at Epson, has been as well. All of our engineers have had great experiences when they have called for support and training.
“We would recommend Epson robots to other manufacturers all day, any day.”
For more information on assembly robots, click www.epsonrobots.com.
For more information on assembly robots, visit www.assemblymag.com to read these articles:
New Software Makes Robots Easier to Deploy
Flexible Feeder Solves Assembly Challenge
You must have JavaScript enabled to enjoy a limited number of articles over the next 30 days.
On Demand Connecting shop floor tools to a manufacturing execution system is critical to error-proofing assembly processes, improving quality control, and lowering defect and scrap rates. Join Torrence Williams, Partnerships Manager for Pico MES, and Dan Smith, VP of Sales for Kolver Tools, as they discuss an easier path for manufacturers to start connecting their factory floor.
On Demand This topic is something that challenges each of us every day that we go to work. This talk is about change and why it works and why it fails. It is focused on manufacturing facilities, because that is where the author has spent most of his working life.
Copyright ©2023. All Rights Reserved BNP Media.
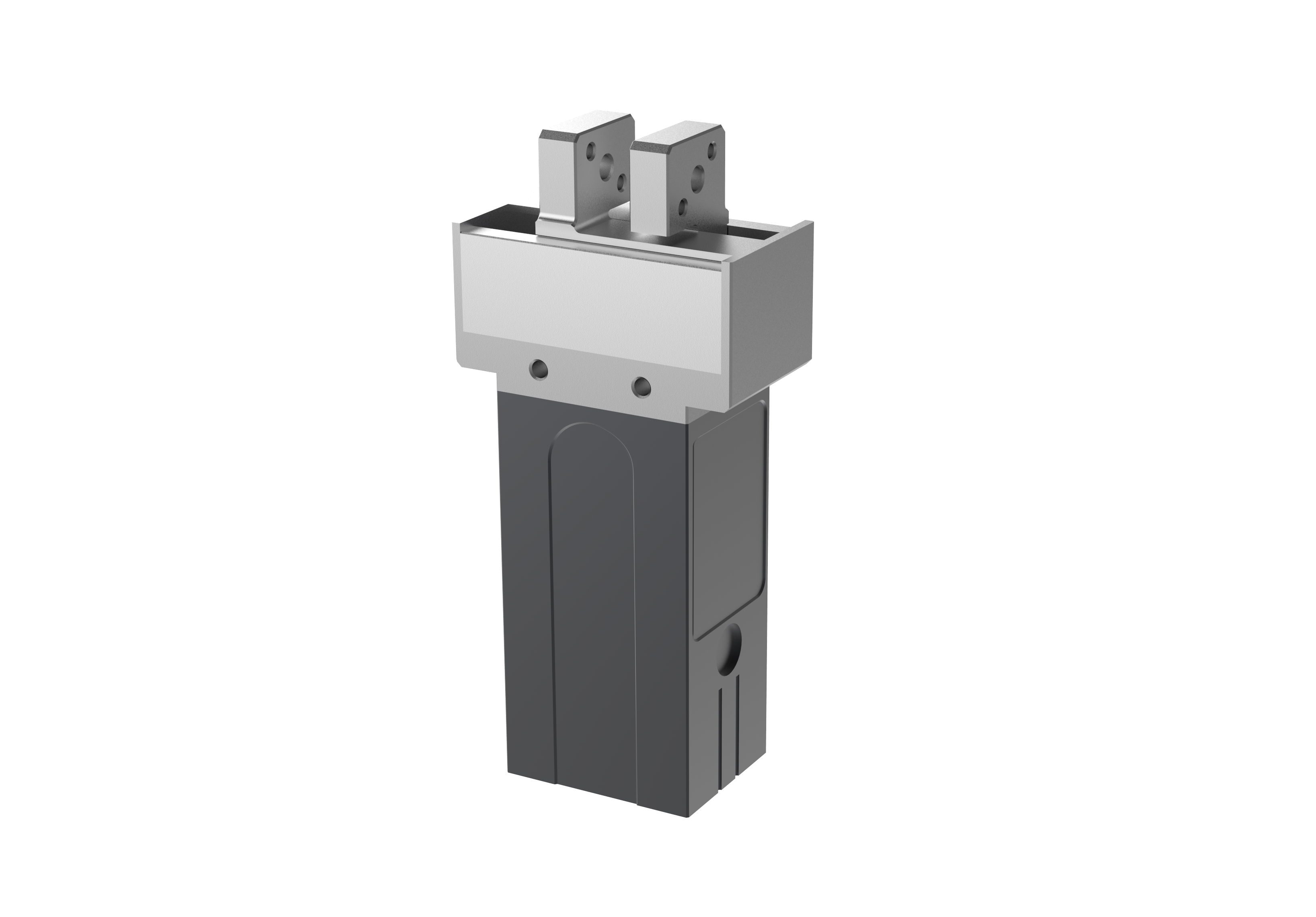
25kg Cobot Design, CMS, Hosting & Web Development :: ePublishing