Due to the slope of the lot and site work that took place before builder Mike Guertin purchased the lot for the Rhode Island Fine Homebuilding House, he only had to dig down 18 in. for the conventionally formed footings. After the foundation is poured, he will truck in dirt to backfill the north and west sides of the foundation, bringing the grade to full height along the foundation walls. The south- and east-facing walls will remain exposed and create a walkout basement. This will offer the homeowners direct access between the yard and the basement and more flexible use of the basement should they wish to finish it in the future. But it also presents some complications for the builder. With part of the foundation below the frost line and part with the footings just 20 in. below grade, the foundation is a hybrid of a traditional frost-protected foundation and a frost-protected shallow foundation.
Guertin has chosen to use insulated concrete forms (ICFs) for the foundation walls. Among the reasons he likes ICFs is that they don’t require separate formwork. They’re installed easily and quickly by a pair of competent carpenters and help keep the project on schedule by eliminating the need to schedule a foundation subcontractor. Unlike board forms that limit the basement headroom to about 7 ft. 8 in., the modular nature of ICFs lets Guertin stack blocks for a full-height 8-ft. basement ceiling. Perhaps foremost among the advantages of using ICFs is that they inherently address the shortcoming of most foundations: no insulation. By using rigid insulation as the form, the insulation becomes part of the wall, and there are no forms for Guertin to strip off after the pour. Many ICFs provide an R-value of about R-20. The Amvic 3.30 blocks chosen for the FHB House have thicker foam than most and provide R-30 insulation and a 6-in.-wide concrete core. Even with this integrated insulation, the exterior of the footings and below-grade portions of walls on the walkout sides of the basement require an additional 21⁄2 in. of rigid EPS to circumvent heat loss. 30mm Drainage Cell
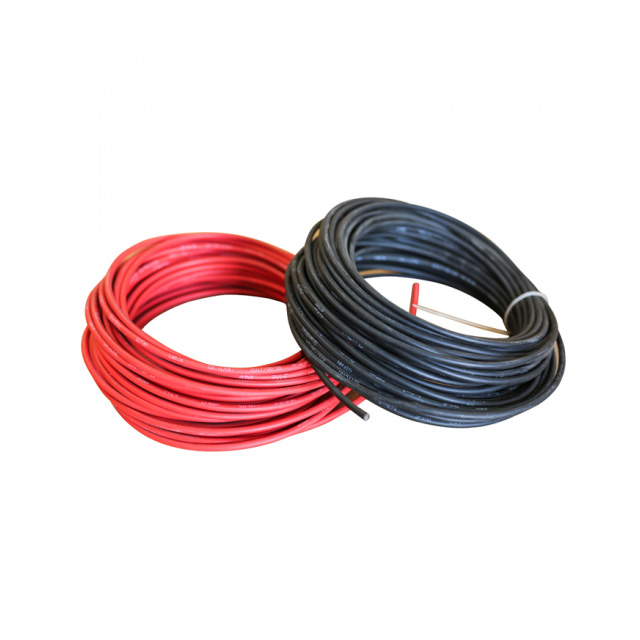
While ICFs use less concrete, they require more steel than conventional foundations, with horizontal and vertical rebar at 24 in. and 16 in. on center, respectively. Even with the rebar, the engineer on this project was concerned about the soil pressure from the north and west sides without backfill on the other sides. His concern related to potential hingepoints, weaknesses at connections of different assemblies—in this case, at the junctions of wood and ICF walls. The original plan was to stick-frame the walkout portions of the basement to “future proof” the basement by providing flexibility for window arrangements and door locations. To allay the engineer’s concerns, however, the plan was modified to use ICF construction everywhere in the foundation except for a small area around the windows on the south side.
ICFs require special treatment on both the exterior and the interior because of their foam faces. Inside, code requires that a thermal barrier or ignition barrier be installed over the foam. Here, it will be CertainTeed drywall. On the exterior, Guertin will use a belt-and-suspenders approach to protect the foam. First, he will cover it from the top of the ICF down over the footings with ProtectoWrap’s Protecto Universal Primer-Free Membrane, which serves as an ICF waterproofing membrane. Next, he will install a dimple mat. This sheet provides drainage space, eliminating hydrostatic pressure, and serves to protect the waterproofing membrane from damage during backfilling.
In a high-performance house, Joe Lstiburek of Building Science Corporation recommends insulating basements north of the Mason-Dixon Line with R-10 subslab insulation and R-20 foundation insulation. The FHB House’s ICFs exceed his basement guideline. To insulate the 4-in.-thick concrete slab, Guertin is using 21⁄2 in. of EPS rigid foam, which provides R-12.5. The Amvic Silverboard under the slab has a polypropylene lamination on both sides that improves durability in this application. A 6-mil poly vapor-and-gas barrier goes over the foam. All seams are taped, and the ends of the poly sheets turn up the ICFs and are taped as well.
It’s important that the insulation and vapor barriers be continuous, so slab penetrations have to be considered carefully. The footings beneath the basement columns aren’t continuous with the slab. By forming the top of the footings 21⁄2 in. below the bottom edge of the slab, there is room to continue the subslab foam over the footings and to tape the vapor barrier to the columns.
A good gravel base ensures that the slab performs as intended. The insulation rests on 4 in. of compacted 3⁄4-in. crushed stone. This base serves several functions: It’s easy to level, it’s a capillary break, and it provides a space for water and soil gases such as radon to move horizontally and to collect in the perforated perimeter-drain pipe. The perimeter drain carries water to daylight well past the house through a sloped drain. A vertical riser from the perimeter-drain loop passes through the slab in the northwest corner of the house and terminates through the roof. The stack effect within the riser induces a slight negative pressure in the perimeter-drain loop. In his region, Guertin has found that a passive vent and a subslab plastic vapor barrier generally control radon levels in the house. If radon levels rise to the EPA’s action level (more than 4 picocuries per liter), adding a continuously running mechanical fan in the riser should correct the problem.
Find more details about the construction of the Rhode Island FHB House foundation:
Sign up for eletters today and get the latest how-to from Fine Homebuilding, plus special offers.
Looks great. Just two thoughts. 1. I understand the best place for the drain pipe is on the footing as opposed two next to the footing. A convex "ribbon" of mortar at the retaining wall and footing seam could help keep water from undermining that joint. The reasoning I've read was the pipe will catch the water earlier and it provides great resistance to lateral movement of the footing. 2. I've had better finished slab results by placing 2 inches of course sand or fine gravel below the slab and above the insulating board. This allows the water in the concrete a place to go and slowly evaporate instead of puddling on the surface making it very difficult to finish in a timely manner and the surface water could weaken the top of slab significantly. Any thoughts or comments are appreciated. Thank You, Bob Bob Di Janni Custom Homes Inc. Santa Fe, NM
A footing drain pipe usually goes alongside the footing rather than on top. The important thing is to have it below the slab level so water is drained away
The layer of sand is called a blotter layer. It has been determined by building scientists to be detrimental to moisture control. Ideally the insulation and plastic vapor barrier should be in direct contact with the underside of the slab. The blotter layer can become a collection area for water. The water will migrate through the slab as vapor elevating humidity in the house. You are right that the sand helps collect the excess bleed water making slab finishing easier and quicker but the downside of installing the sand is for the life of the house
I'm enjoying the ProHome project. I'd like to hear your deliberations on using the ICFs for an unfinished basement when the interior foam requires a thermal/ignition barrier. Will you install electrical in the basement exterior walls prior to drywall? For the unfinished basement, it would seem the added initial cost of the ICFs with interior drywall would be substantially higher than an exterior foam insulation with exposed concrete interior wall.
I don't understand the part about " The footings beneath the basement columns aren’t continuous with the slab. By forming the top of the footings 21⁄2 in. below the bottom edge of the slab, there is room to continue the subslab foam over the footings and to tape the vapor barrier to the columns."
It sounds like the slab insulation is continuous over the column footings, then the slab over that and the columns...? Or maybe a small hole in the sub-slab insulation, so the columns can poke through and bear on their footings? Or?
Reply to BobboMax: I positioned drywall buckets on top of the footings at the two locations where the columns were to be located. We installed foam and then poured the slab. After the columns were installed between the top of the footing and the beam I fit foam around the base of the columns, taped in the plastic sheet and then mixed a sack of concrete to finish the slab around the columns.
How are dimple mats attached to ICF? I'm also wondering what the detail looks like where a dimple mat is fastened to a home basement foundation wall underneath an attached garage slab, since the top normally terminates above grade with some sort of termination bar.
The R 30 value, when making comparisons, is only valid for a constant inside house temperature and doesn't give a true representation of the homes's comfort or energy efficiency.
When the thermostat is lowered such as when one leaves for work, that concrete, which is still somewhat warm, because half of the insulation is on the outside, gives up its heat for many hours. When one returns home, it takes many hours to reheat that concrete. This isn't a problem in moderate climates, but in colder climates, it is. It can take 20 hours to reheat the concrete in a vacation home that is used in the winter. Arrive on Friday night and the basement is just getting warm by Saturday afternoon. ...and that furnace is sucking energy the whole time to reheat the concrete. It is much more efficient to heat air than it is to heat concrete.--I speak from experience. My buddy made this mistake.
Don't be fooled by the sales literature saying that the basement is already insulated and ready for finishing. It is absolutely necessary to add more insulation to the inside of the basement walls.
Trusted, comprehensive guidance from the pros for working with concrete and masonry
View All Project Guides »
Become a member and get unlimited site access, including the Foundations and Masonry Work Project Guide.
Get home building tips, offers, and expert advice in your inbox
© 2023 The Taunton Press, Inc. All rights reserved.
Get home building tips, offers, and expert advice in your inbox
Become a member and get instant access to thousands of videos, how-tos, tool reviews, and design features.
Start your subscription today and save up to 70%
Get complete site access to expert advice, how-to videos, Code Check, and more, plus the print magazine.

Drain Channel Already a member? Log in